Precision in Pressure: How Leak Testing Fuels Safer Products
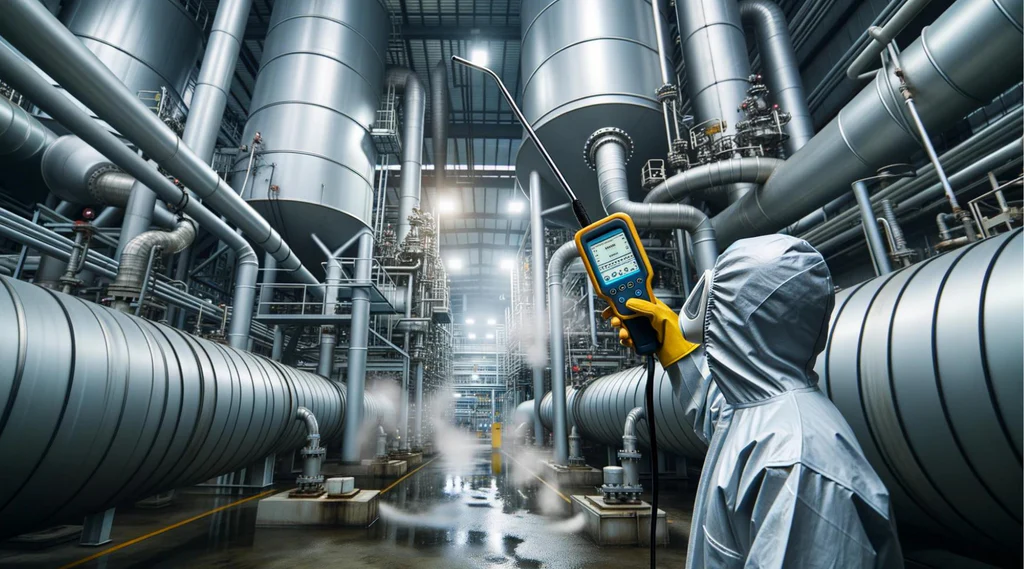
Why Leak Testing Matters in Manufacturing
The significance of leak testing in today’s manufacturing environment extends beyond simply ensuring a shiny product leaves the production line. In many ways, it is a silent guardian of safety and quality, ensuring every tank, connector, enclosure, or seal is fit for its intended purpose. Even the most minor undetected leak can translate to product failure, warranty claims, and damaging legal disputes when overlooked or inadequately executed. More advanced systems quickly replace techniques that seemed sufficient only a few years ago in response to rising complexity and stakes. Manufacturers recognize the strategic value of integrating precision leak testing equipment into all production phases—from prototyping and product development to large-scale assembly and before final shipping. For example, undetected leaks in mission-critical industries such as aerospace or pharmaceuticals could result in environmental exposure, hazardous spills, or ineffective dosage delivery. Early detection through robust leak testing is proven to significantly minimize these risks and financial losses by catching flaws before they can propagate into larger issues downstream. A comprehensive report on leak testing dynamics indicates that integrating stringent leak detection at early manufacturing stages can save lives and shield organizations from costly recalls and irreversible brand damage. The ripple effect of effective leak testing is also seen in increased customer trust. In a competitive marketplace, consumers and regulators pay close attention to product recalls, malfunctions, and safety records—events often stem from undetected leaks. By building leak integrity into the design and quality assurance pipeline, companies can deliver durable, trustworthy products and reduce after-market maintenance costs.
Standard Methods for Detecting Leaks
Different products, environments, and regulations require different leak detection methods, each with unique strengths, limitations, and applications. Understanding these options helps companies select the right solution for their quality assurance goals:
- Pressure Decay: Widely adopted for mass production, this automated method introduces air or inert gas into a sealed part and monitors the internal pressure. Even a slow drop in pressure over a few seconds can reveal a leak that would otherwise escape visual checks. Pressure decay testing balances accuracy with speed, making it indispensable for electronics, valves, batteries, and food packaging.
- Helium Leak Detection: This highly sensitive technique fills or sweeps a component with helium and then uses a mass spectrometer to detect escaping gas. Since helium molecules are tiny, this method reveals even micro-leaks. It is the gold standard for systems where any ingress or egress can pose significant risks—for instance, in medical implants, MRI machines, or satellite controls.
- Bubble Testing: The image is simple but effective: a part is submerged in water and pressurized internally. Visibly rising bubbles from the test area identify leak locations. Though not as sensitive as instrument-based methods, bubble testing is favored for its affordability and ease in sectors like plumbing or low-pressure hydraulic systems. It works exceptionally well for irregular shapes and quick troubleshooting.
- Ultrasonic Leak Detection: These advanced detectors “listen” for acoustic signatures generated by escaping gas or air. Minor leaks create distinct frequencies, allowing technicians to pinpoint locations in complex or inaccessible assemblies. Ultrasonic devices are now standard in automotive assembly lines, large liquid tanks, and HVAC ductwork, significantly improving overall defect identification rates.
Often, manufacturers use more than one method for confirmation or at different stages of the production process. Ongoing research and real-world industry feedback support these techniques’ continuous evolution and hybridization.
Industry Case Studies: Leak Testing in Action
Illustrative real-world case studies reveal why leak testing is a non-negotiable aspect of modern manufacturing. In the automotive industry, for example, leaks in fuel systems, cooling loops, or braking assemblies can trigger large-scale recalls, fines, and loss of consumer confidence. Failure to detect a small crack during initial assembly could escalate to complete system failure on the road, risking property and lives. The stakes are even higher for the medical sector. Here, every leak carries the potential for infection, drug delivery errors, or compromised sterility. Infusion pumps, catheters, and endoscopes must be completely leak-proof, especially when reprocessed between uses. Routine leak testing is now a standard requirement for cleaning and reprocessing reusable devices. This protocol sharply reduces the risk of cross-contamination and regulatory non-compliance. Companies that have embedded thorough leak testing into each step of product development and cleaning have reported marked patient risk and regulatory penalty declines, underscoring the value of consistent, validated leak detection practices. Even beyond safety, robust leak testing supports sustainability initiatives by reducing waste and enabling recycling of components that pass inspection. Environmental sectors, for instance, rely on leak-free containment systems for handling chemicals and waste, making testing standards a driver for both safety and ecological responsibility.
Regulatory Drivers and Standards
With governments and industry associations worldwide tightening rules around environmental impact, product safety, and consumer rights, robust leak detection has transitioned from best practice to mandatory. Organizations such as the FDA, CE, and ISO no longer only recommend leak testing—they require it for compliance and market access. ISO 13485, ISO/TS 16949, and ISO 9001 all lay out stringent requirements for test limits, system validation, and traceability, and compliance with these standards is periodically audited. These standards don’t just demand accurate leak testing. They also specify procedures for documentation, calibration records, operator training, and risk assessments. As a result, manufacturers are moving toward highly automated test systems that generate instant, exportable reports and securely store all data. Such transparency streamlines audits, accelerates certifications, and assures stakeholders that every item meets quality and safety expectations. As regulations evolve, manufacturers proactively adopting strong leak-testing frameworks are best prepared to meet new challenges and rising consumer demands.
Emerging Technologies in Leak Detection
In recent years, there has been a digital revolution in leak detection. High-resolution digital pressure sensors now outperform older analog devices, capturing anomalies that might once have gone unnoticed. At the same time, incorporating machine learning and artificial intelligence into test system software adapts inspection settings in real-time, learning from past data to predict and prevent test failures. Adopting Internet of Things (IoT) sensor arrays has also transformed maintenance. Manufacturers can now monitor thousands of components simultaneously, triggering service calls automatically when a potential pattern of leaks is detected. These innovative systems benefit operations of every size, as automated data capture allows for root cause analysis, predictive maintenance, and optimization. The pace of these technological advancements ensures that what is considered state-of-the-art today will likely become the industry baseline tomorrow.
Real-World Challenges and Solutions
Despite the impressive progress, leak detection is not without its obstacles. Pressure and temperature fluctuations on the factory floor introduce noise into tests, sometimes leading to false results. High-speed production can compound challenges by reducing inspection time and increasing the demand for precise but rapid measurements. Additionally, some components may require specially designed fixtures to ensure complete sealing during the test.
Manufacturers address these challenges by creating standardized, climate-controlled test cells, enhancing operator training, and deploying redundant checks at critical points. Integrating multiple leak detection techniques, such as ultrasonic validation after a pressure decay failure, is now standard for high-stakes components. Regular review of these protocols, informed by industry research and shared case studies, helps keep practices sharp and outcomes reliable.
Key Considerations for Choosing a Leak Test Method
- Application Requirements: Different industries and products dictate unique sensitivities—from micro-leaks in electronic chips to visible leaks in automotive fuel tanks. Test limits and materials should mirror the risk tolerance for the product’s use case.
- Production Speed: High-throughput lines benefit most from automated and inline systems, which must be calibrated for rapid, repeated assessment without sacrificing accuracy.
- Cost vs. Sensitivity: It’s essential to balance the up-front investment in advanced leak detection with potential cost savings, regulatory benefits, and brand protection over a product’s lifecycle.
- Human vs. Machine: While automation dominates high-volume runs, human expertise remains vital for complex, bespoke, or new product verification, blending the best of both worlds for thorough, reliable results.
Decisions on method selection should involve cross-functional teams weighing all technical, operational, and business factors to determine the best fit.
Future Trends in Leak Testing
As consumer expectations and regulatory requirements continue to rise, leak testing is evolving to keep pace. There’s a shift towards digital twins, remote diagnostics, cloud-based test monitoring, and mobile reporting dashboards. This interconnectedness allows manufacturers unprecedented oversight and flexibility in managing distributed production sites. Environmental responsibility is also front and center, driving innovation in sustainable test media and cutting the waste associated with disposable sensors and consumables. These advances allow manufacturers to keep product quality, resource consumption low, and compliance on track, ultimately benefiting consumers and industries worldwide.